Większość osób chcących wejść w branżę druku 3D w pierwszej kolejności myśli albo o produkcji lub sprzedaży drukarek 3D lub usług na nich wykonywanych. Sprytniejsi biorą się za sprzedaż filamentów, a ostatnio jak grzyby po deszczu zaczynają się pojawiać mikrofirmy, oferujące w swoich „centrach szkoleniowych” usługi warsztatów z podstaw druku 3D w technologii FDM. Tymczasem drukarki 3D oferują bez porównania więcej możliwości i nie muszą być to wcale rzeczy wyjątkowo innowacyjne czy zmieniające oblicze świata… W listopadzie zeszłego roku opisywałem projekt firmy Additive Solutions, oferującej na Kickstarterze kolorowe obudowy do MakerBot Replicatorów 2. Pomysł – tak banalny w swoim założeniu, pozwolił firmie zdobyć 2,5 raza wyższy poziom dofinansowania od wnioskowanego i z powodzeniem funkcjonuje do dziś. Firma Ideal Jacobs Corporation wyszła z podobnego założenia, ale w przeciwieństwie do Additive Solutions nie ograniczała się do jednego modelu drukarki 3D. Zamiast tworzenia spersonalizowanych obudów, postanowiła rozwiązać jeden z największych problemów RepRapów – kwestii przyklejania wydruków do stołu roboczego.
Od samego początku istnienia RepRapów jednym z kluczowych problemów była przyczepność drukowanych modeli do podłoża. W celu jego rozwiązania stosuje się tu kilka metod:
- druk 3D na podgrzewanym stole (PLA i ABS)
- druk 3D na niebieskiej taśmie (PLA)
- druk 3D na taśmie Kaptonowej
- druk 3D na tzw. „soku z ABS” (kawałków ABS rozpuszczonych w acetonie)
- druk 3D na stole smarowanym klejem wodno-rozpuszczalnym
- druk 3D na stole pokrytym warstwą spray`a do włosów.
Każda z powyższych metod ma swoje dobre i złe strony. Najlepszym sposobem jest stosowanie podgrzewanego stołu, ale wiąże się to z większymi kosztami urządzenia (inna sprawa, że z ABS w ogóle nie powinno się drukować bez podgrzewanego stołu). Używanie taśm wymaga ich ciągłego dokupowania oraz naklejania w odpowiedni sposób. Sok z ABS nie jest przyjazny dla środowiska naturalnego i zdrowia, z kolei klej lub lakier do włosów bywają zawodne przy określonym rodzaju materiałów. Tak czy inaczej – nie licząc podgrzewanego stołu wszystkie powyższe rozwiązania mają charakter amatorski i umożliwiając pracę z drukarką 3D na swój sposób ją utrudniają.
Są firmy, które rozwiązały ten sposób jeszcze inaczej – Up! i Zortrax stosują stoły z perforowaną powierzchnią, które nie wymagają niczego poza raftu (warstwy początkowej wydruku, którą odrywa się od wydrukowanego modelu. To rozwiązanie sprawdza się moim zdaniem najlepiej, ponieważ nie wymaga żadnych działań względem stołu roboczego poprzedzających wydruk – wystarczy po prostu wgrać plik z projektem i rozpocząć drukowanie (stół musi być oczywiście wcześniej podgrzany co jest standardem w drukarkach 3D obydwu firm). Druk 3D pierwszej warstwy odbywa się w dokładnie tym samym tempie co pozostałych, nie trzeba zwalniać urządzenia do absurdalnie wolnej prędkości aby się ona przypadkiem nie odlepiła.
BuildTak
Trudno mi powiedzieć dlaczego pozostali producenci drukarek 3D nie korzystają z tego rozwiązania, stosując namiętnie stoły wykonane ze szkła, akrylu, czy blachy? Amerykańska firma Ideal Jacobs Corporation również postanowiła nie wnikać w ten temat, a zamiast tego spróbowała na tym zarobić. Tak oto powstał BuildTak – specjalna podkładka na stoły robocze do drukarek 3D, umożliwiająca druk 3D bez konieczności stosowania innych materiałów pomocniczych (za wyjątkiem oczywiście podgrzewanego stołu).
Sprzedażą BuildTak w Polsce zajmuje się Get3D, które udostępniło mi jedną podkładkę do testów. Przyznam, iż ambicje miałem spore – chciałem wypróbować ją na kilku rodzajach materiałów, próby udokumentować na na kilkudziesięciu zdjęciach, spisując po drodze wszystkie możliwe ustawienia drukarki 3D. Tymczasem już podczas pierwszego wydruku wiedziałem, że to bezcelowe… BuildTak jest po prostu świetny – wszystkie problemy jakie miałem przy rozpoczynaniu wydruków po prostu zniknęły. Testując podkładkę na Prime 3D z Monkeyfab, po raz pierwszy czułem się jakbym drukował na Up!`ie lub Zortraxie – po prostu włączałem wydruk i on się drukował…
Pracę z BuildTakiem bardzo dobrze opisał również Krzysztof Dymianiuk na MójRepRap oraz Łukasz Czuba na blogu Rabbitów. Wnioski są wszędzie dokładnie te same – podkładka świetnie sprawuje się w wydrukach wykonywanych z PLA na zimnym stole, podobnie w przypadku ABS, choć tu pojawiają się problemy przy ich zdejmowaniu. Łukasz ponadto przetestował z powodzeniem Laywood, Laybrick a nawet nylon, choć przy tym ostatnim nie wszystko już szło tak jak trzeba.
Instalacja BuildTak
BuildTak występuje w kilku formatach: 139 x 139 mm, 165 x 254 mm, 203 x 203 mm, 254 x 228 mm, 254 x 254 mm i w zależności od rozmiaru kosztuje od 24,00 PLN do 68,00 PLN (brutto). Ja do Prime`a otrzymałem 203 x 203 mm. Montaż podkładki jest prosty, choć należy tu skorzystać ze starej sprawdzonej metody:
- najpierw stół dokładnie czyścimy za pomocą spirytusu, acetonu lub innego odtłuszczacza
- następnie odklejamy kawałek folii zabezpieczającej ze spodu i przyklejamy początek podkładki u szczytu stołu
- stopniowo wyklejamy cały stół odklejając folię ze spodu; w trakcie wyklejania należy dociskać kolejne fragmenty przyklejanej podkładki tak, aby nie dopuścić do powstawania pęcherzyków powietrza pomiędzy stołem a podkładką.


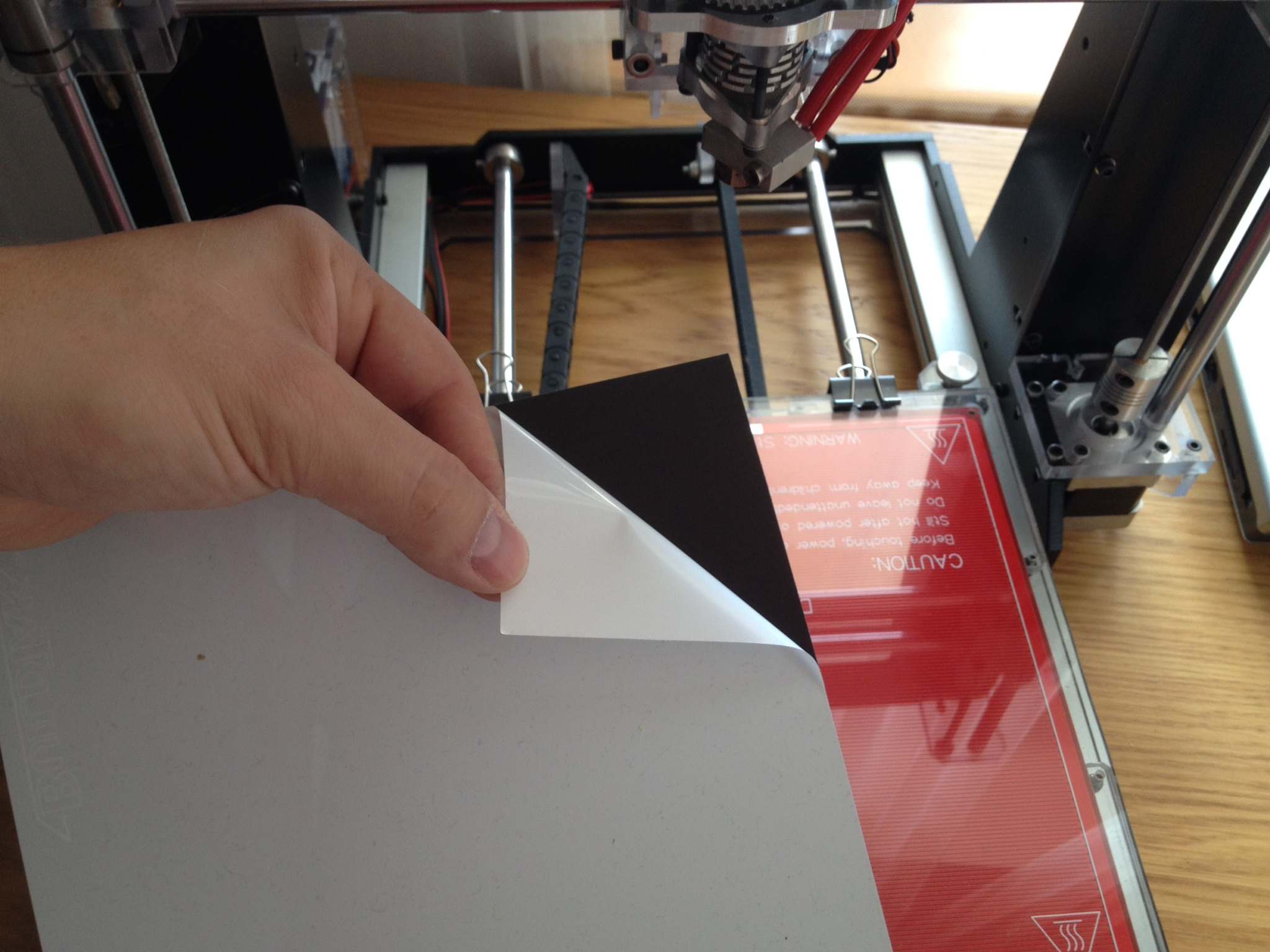





Gdy BuildTak jest już naklejony należy na nowo wypoziomować stół względem głowicy drukującej. W przypadku Prime poziom stołu podniósł się o tyle, że nie miałem już możliwości regulacji jego wysokości i musiałem podnieść „punkt zero” w osi Z. Wystarczyło… podłożyć 1-groszówkę pod endstopa
Jest to o tyle ważne, gdyż BuildTak jest wykonany z tworzywa sztucznego i jeżeli dociśniemy do niego rozgrzaną do 200°C – 250°C głowicę, to po prostu ją w tym miejscu stopimy. Gdy mamy już ustawiony „poziom zero”, poziomujemy cały stół (w przypadku Prime świetną i prostą metodę na to opisał Krzysiek Matusiewicz) i możemy rozpocząć drukowanie.
Praca z BuildTak
Jeśli chodzi o PLA to jest ona łatwa, prosta i przyjemna. Wystarczy włączyć drukowanie i materiał przykleja się z powodzeniem na zimnym stole. W testach korzystałem z błękitnego Noviplastu z Get3D. Zacząłem od prostych modeli, jak koparka LITTLE BUILDER, czy różnego rodzaju case`y na telefony. Po pięciu pomyślnych wydrukach postanowiłem spróbować wydrukować coś naprawdę trudnego – Lament Configuration Case. Filament przylegał bez żadnego problemu – i to wciąż na zimnym stole.

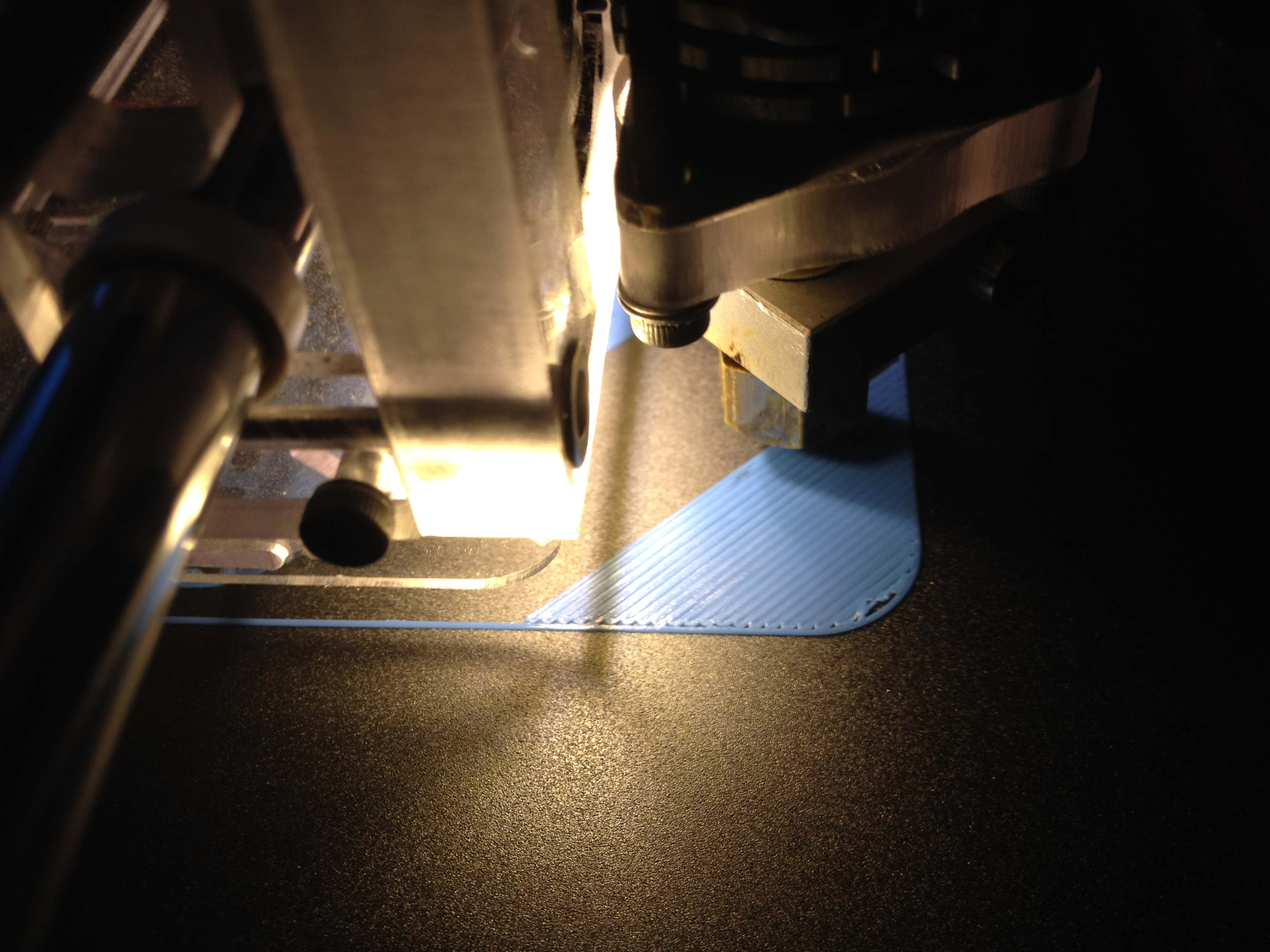




Kolejnym materiałem, który wziąłem na próbę był t-glase z taulmana. To bardzo problematyczny materiał, z którego mimo kilku wcześniejszych prób nie udało mi się nigdy nic wydrukować. t-glase albo nie przyczepiał się do stołu wcale (zimne lub rozgrzane szkło – suche lub smarowane klejem), albo po nadrukowaniu 1-2 warstw, przy kolejnej głowica zrywała to co wydrukowała wcześniej. Na BuildTak udało się to już za drugim podejściem. Kluczowe okazały się prędkość i odpowiednie wypoziomowanie stołu (więcej informacji na ten temat w recenzji t-glase). Tak czy inaczej, najbardziej ekstremalny z materiałów do druku 3D z jakim miałem styczność został okiełznany i to w dużej mierze za sprawą podkładki!

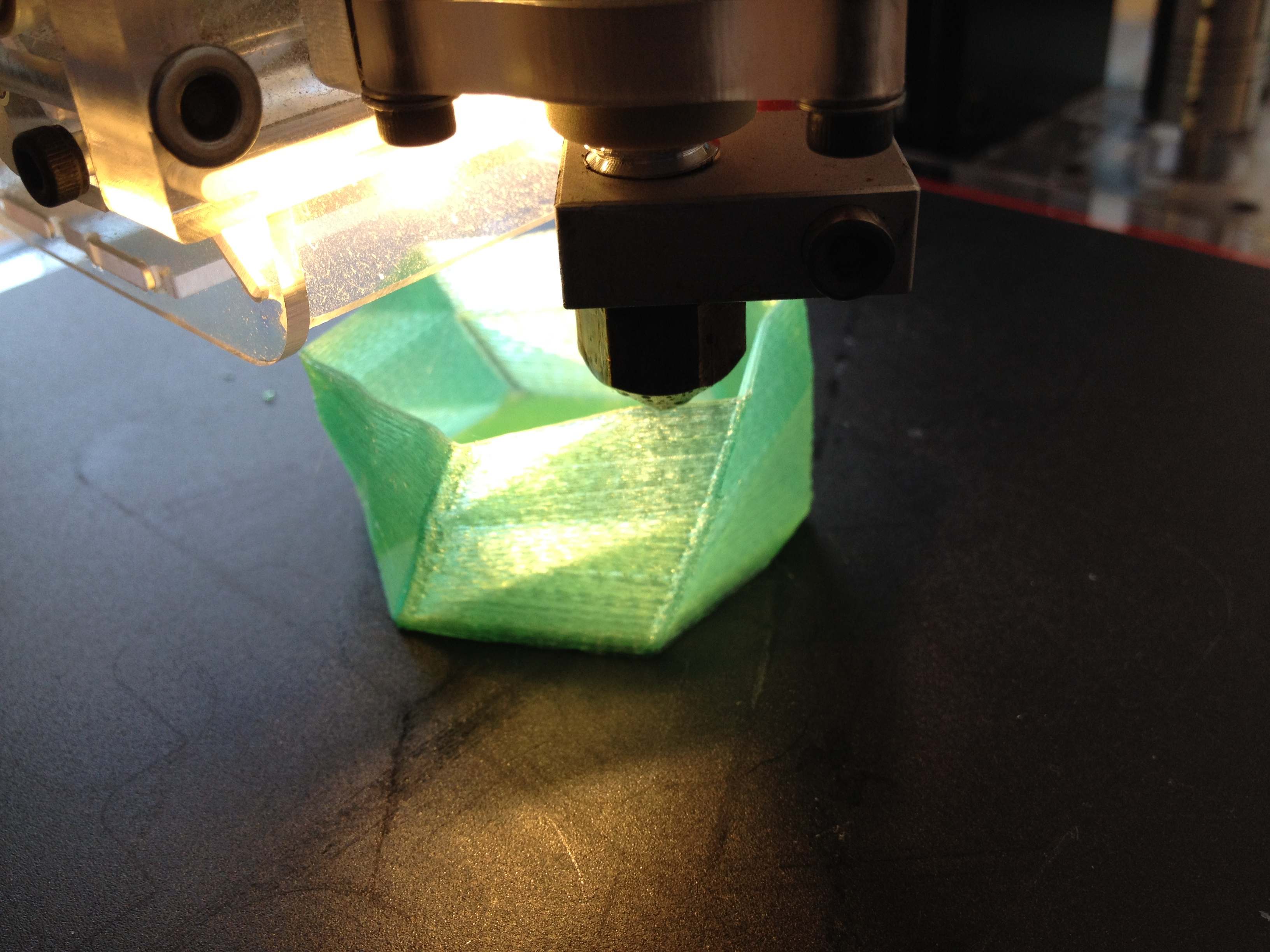
Jeśli chodzi o zdejmowanie wydruków, to w przypadku PLA oraz t-glase nie ma z tym większego problemu – w skrajnych przypadkach trzeba użyć szpachelki i delikatnie podważyć. Jeżeli głowica będzie wyjątkowo nisko stołu i „dociśnie” plastik do stołu, przy odrywaniu wydruku z podkładki, jego kawałek może niestety zostać na stole. Tak było w przypadku „Lamentu” gdzie drobne, pojedyncze fragmenty wydruku ukruszyły się. Bardzo ciekawie prezentuje się za to spód wydruków – jest gładki, choć w dotyku da się wyczuć delikatną ziarnistość, taką samą jak powierzchnia podkładki.

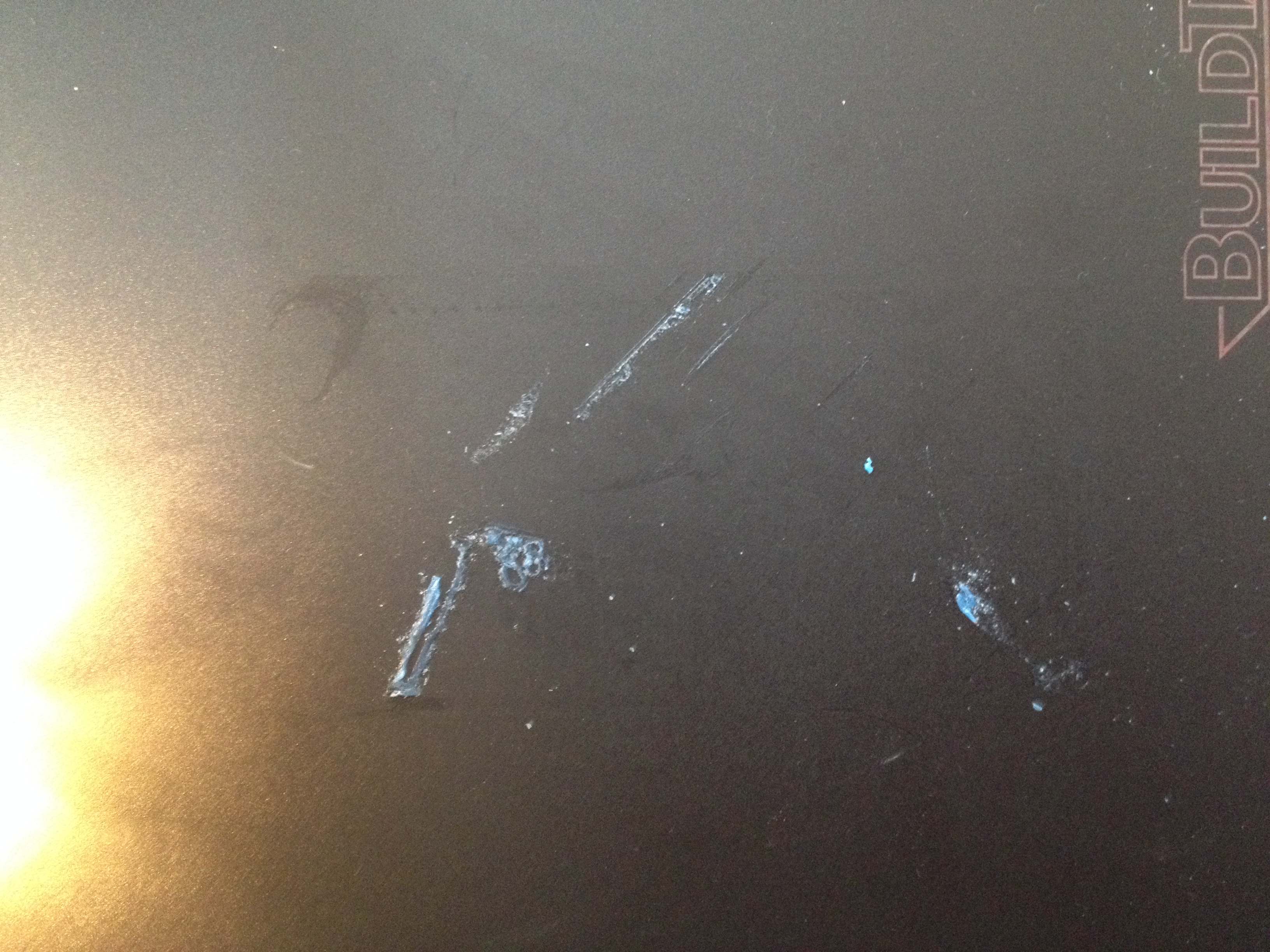

Do tej pory nie zdążyłem jeszcze testować ABS, ale z relacji Krzysztofa i Łukasza wiadomo, iż problemy ze ściąganiem wydruków są bez porównania większe i wymagają odpowiedniej techniki. Jeżeli będzie się to robić nieumiejętnie, można zniszczyć albo wydruk albo samą podkładkę.
Wady BuildTak
Tak naprawdę jest tylko jedna – podkładka ma ograniczoną żywotność i z biegiem czasu po prostu się zużywa. Po wydrukach zostają ślady – smugi, które można usunąć albo zeskrobując je szpachelką, albo próbować zetrzeć jakimś tradycyjnym środkiem czyszczącym do szyb. Do czyszczenia BuildTak nie wolno używać acetonu lub spirytusu, ponieważ można go uszkodzić. Kolejna sprawa to ściąganie wydruków z ABS – Krzysztof opisał, iż po pięciu dniach intensywnego używania podkładki, odkształciła się ona i zrobiła się w niej dziura od zbyt mocnego operowania szpachelką przy ściąganiu wydruków. W końcu nieumiejętne lub niefrasobliwe kalibrowanie głowicy drukującej w trakcie druku 3D może spowodować, iż rozgrzana głowica nadtopi fragment podkładki.
Podsumowanie
BuildTak – mimo swoich pojedynczych wad i niedoskonałości jest wybawieniem. Praca z podkładką znacząco podnosi komfort pracy na drukarce 3D klasy RepRap i poprawia jakość wydruków. Odpadają eksperymenty z różnego rodzaju chemikaliami, precyzyjne wyklejanie stołów taśmami lub poszukiwania właściwego kleju w sklepach z artykułami biurowymi. Jeżeli uda się utrzymać żywotność BuildTak na okres 3 miesięcy, cykliczny wydatek rzędu 40-60 złotych powinien w pełni się zwrócić.